How AP automation helps manufacturing companies reduce costs & improve efficiency
Financial management is critical in the manufacturing sector, where razor-thin margins make effective cost and efficiency optimization essential to success. However, traditional paper-based accounts payable (AP) processes create bottlenecks that strain resources. As manufacturing evolves to adopt smart technologies, AP automation has emerged as a game-changing digital transformation for manufacturers.
By automating repetitive and time-consuming invoice and payment tasks, AP automation enables substantial cost reduction and efficiency gains. This article will demystify AP automation in the manufacturing context and showcase real-world examples of its financial and operational benefits. For manufacturing companies struggling with rising costs and inefficient legacy financial operations, AP automation presents a strategic opportunity to boost profitability and productivity.
AP automation for manufacturers
What is AP automation? A manufacturing perspective
AP automation is the digital transformation of paper-intensive accounts payable systems into streamlined digital workflows. By extracting invoice data, integrating it into centralized platforms, automating approvals and integrating with ERPs, AP automation eliminates manual tasks.
In manufacturing, processes like recording supplier invoices, approving or adjusting entries, routing invoices and issuing payments are rife for automation. Doing so with intelligent software allows manufacturing companies to significantly optimize their purchase-to-pay cycles.
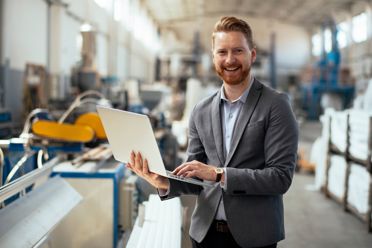
Traditional vs automated AP processes in manufacturing settings
For manufacturing firms still relying on manual AP systems, costs and delays quickly compound:
- Lost or misfiled invoices must be tracked down before starting approvals, wasting days of effort.
- Routing invoices for physical signatures is time-consuming and risks further delays or errors.
- No centralized oversight means maverick spend goes unseen, while rush payments raise compliance risks.
- Entering and posting invoice data by hand into separate systems like ERPs allows errors to creep in.
Conversely, automated AP platforms apply digital workflows with complete invoice visibility:
- eInvoices are extracted to a single searchable repository with customizable business rules.
- Automated, conditional routing with digital approval controls replace physical signature chasing.
- Centralized reporting provides complete AP spend visibility to prevent duplicated or rogue spend.
- Native ERP integrations synchronize approved invoice data to minimize manual re-entry.
Cutting costs effectively with AP automation
How AP automation streamlines cost management
AP automation gives manufacturers the tools to actively cut costs across the procure-to-pay process:
Early payment discounts can be captured based on real-time visibility into invoices pending approval or payment.
Duplicate payments are eliminated via digital invoice matching algorithms and central reporting.
Maverick spend gets reined in with executive visibility into purchases across departments and facilities.
Enforcing compliance while eliminating inefficiencies lets manufacturers stretch budgets significantly further.
Real-world cost savings: Case studies from the manufacturing industry
Manufacturers around the world are already quantifying dramatic cost savings results after implementing AP automation to optimize their finances:
Increased invoice processing
Companies like NIC Global boosted invoice handling from 650 to 800 per week, enhancing productivity without expanding staff.
Reduced operational costs
Implementation led to notable savings in postage and printing, and enabled capturing early payment discounts from vendors.
Enhanced process efficiency
Automated workflows streamlined approvals and issue resolution, coupled with 24/7 invoice access and automated alerts, preventing delays in approvals.
Long-term financial impacts of AP automation
While the immediate, bottom-line cost savings matter, manufacturers stand to unlock deeper strategic value from AP automation over the long term. Improved cost controls and cash visibility enable better-informed investments, negotiated supplier terms and inventory management. Procurement and finance can evolve from scorekeepers to strategists.
As manufacturing becomes faster, leaner and more complex, AP's financial optimization role will only grow. Having the right digital infrastructure via automation becomes imperative to better decision making and profitability.
Boosting operational efficiency through AP automation
Enhancing invoice and payment efficiency
Just as important as saving costs for manufacturers, AP automation speeds up key processing functions to make operations more efficient using:
- Automated data capture and coding to eliminate manual invoice entry
- Rules-based, digital routing for instant approvals
- Direct ERP and supplier integrations to remove transactional bottlenecks
- Real-time reporting and analytics instead of periodic analyses
Such digital enhancements streamline even the highest invoice volumes in manufacturing for significant time savings.
The impact on workforce productivity and resource management
By automatically handling repetitive AP tasks, AP automation lets manufacturers re-allocate administrative resources to more strategic aims. Staff productively shifted from manual data entry or invoice matching to validate exceptions, supply market analysis or optimize relationships.
Combined with the ability to catch duplicate payments or unauthorized purchases earlier, AP automation gives manufacturing executives better visibility to proactively adjust budgets or supply contracts before issues escalate. The same teams and technologies now progress key business initiatives and process improvements instead of performing transactions.
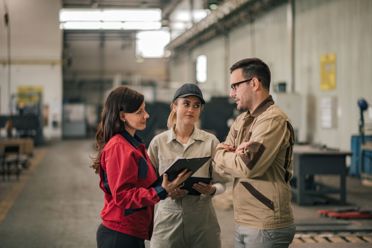
Case examples: Efficiency improvements in manufacturing companies
SMC Corporation, a leader in pneumatics and automation for the manufacturing industry, experienced notable efficiency improvements after migrating their Accounts Payable (AP) processes to the cloud with Medius AP Automation:
- Dramatic reduction in invoice processing time: SMC reduced the time required to process each invoice from 10 minutes to just 2 minutes, significantly speeding up their financial operations.
- High degree of automation achieved: Within four months of deployment, SMC achieved a 70% touchless ratio in their invoice processing, indicating a high level of automation and efficiency.
- Enhanced accessibility and control: The transition to cloud-based AP Automation provided SMC with 24/7 access to their systems on both desktop and mobile devices without needing a VPN, offering greater flexibility and control over their processes.
- Reduced errors and risks: The adoption of Medius AP Automation helped SMC to significantly reduce errors and duplicate payments, and also lowered the risk of fraud and late fees.
These improvements underscore the significant efficiency gains that can be achieved in the manufacturing sector through the adoption of advanced AP automation solutions.
Importance of accuracy and compliance
The role of AP automation in reducing errors and ensuring accuracy
In pricing errors, late payments, duplicate invoices or non-compliant purchases, a single AP misstep risks major financial damage in manufacturing. AP automation minimizes such accuracy risks by applying smart rules and automation at key process checkpoints:
- eInvoice field data gets validated against configured formats, business identifiers, contract rates and recorded chart-of-accounts.
- Invoice batch totals pass three-way matching checks before approvals to spot quantity or rate fluctuations.
- Automated payment confirmations from the ERP to supplier payment network prevent duplicate payments.
Together, these checks and balances structurally improve the accuracy of core AP data - which then flows reliably into other manufacturing operations.
Maintaining regulatory compliance in manufacturing with automated processes
Maintaining regulatory compliance in manufacturing with automated processes is crucial, particularly given the complex requirements surrounding revenue recognition, tax liabilities, financial controls, and more. When accounts payable (AP) tasks remain manual, enforcing every policy can be incredibly challenging.
AP automation introduces a transformative solution by embedding defined rules directly into the digital process. This approach includes establishing role-based approval chains to ensure proper oversight, implementing compliance rule checks during invoice field extraction or three-way matching, and controlling exception workflows for batches that fail validation, thus eliminating the need for manual intervention. By catching compliance breaches before they lead to audits or penalties, AP automation provides a robust and scalable structural safeguard in the manufacturing sector.
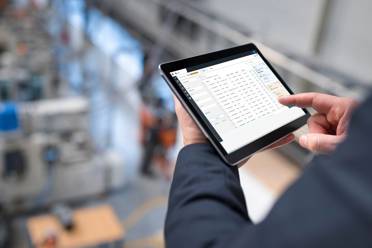
Seamless integration of AP automation and manufacturing systems
Integrating AP automation with existing manufacturing ERP systems
Instead of introducing yet another disconnected system, AP automation platforms integrate natively with major manufacturing ERPs like SAP, Oracle, Infor and Microsoft Dynamics. Standard interfaces eliminate complex custom coding needs during implementation projects.
Moreover, intelligent connectors enable reliable, real-time data flows across finance and ERP systems - avoiding manual rework and synchronization:
- Validated eInvoice data flows directly into the chosen ERP upon approval instead of re-entering into multiple systems.
- Two-way integration means invoice or payment confirmations in the ERP will also update the AP solution.
- Common master data like suppliers and chart-of-accounts is shared, improving downstream reporting accuracy.
The benefits of integration for data consistency
ERP-embedded AP data better aligns planning, inventory or shop floor decisions to actual committed costs and liabilities. When AP resides outside the ERP, latency and order changes lead to distortions between systems over time.
Shared master and transactional data viscosity improves when financial, procurement and operational platforms converge – in turn providing more consistent reporting. Reliable analytics guides everything from cost controls to demand forecasting and margins analysis.
Scaling up: AP automation supporting growth
How AP automation facilitates business growth and scalability in manufacturing
Once AP automation absorbs transactional volume, manufacturing firms gain the capacity to efficiently onboard new facilities, increase orders and handle wider supplier rosters as business grows. Smooth AP scalability ensures no bottlenecks across metrics like:
- Number of invoices processed and paid on time
- Visibility coverage across spend categories
- Continued compliance with company policies & external regulations
- Up-to-date reporting even with volatility
Growing manufacturing firms need the flexibility to scale operations without proportional admin headaches – an advantage automated platforms confer.
Preparing for future technological developments with AP automation
Modern AP automation already interlinks with advanced technologies manufacturers are exploring, whether IoT sensors, logistics telematics, predictive analytics or machine learning. Building API connectivity and nurturing technology partnerships ensures manufacturing companies can smoothly adopt emerging innovations.
While still unlocking substantial efficiency and savings today, AP automation choices should anticipate the accelerating digital future of manufacturing.
Overcoming implementation challenges: A guide for manufacturers
Identifying and addressing challenges in adopting ap automation in manufacturing
Manufacturing leaders must be aware of a few common hurdles that can delay capturing the full benefits of AP automation if not addressed early:
- Customizations to legacy ERP systems that limit integration viability without re-engineering.
- Change management concerns from AP staff fearful of job losses from new technologies.
- Difficulty articulating the hard-dollar ROI value from operational efficiencies.
- Pre-existing supplier contracts with restrictive eInvoice/payment terms.
With upfront communication, testing and phased deployment, manufacturers can overcome most barriers.
Choosing the right ap automation solution for your manufacturing business
Manufacturing has unique demands - from high invoice intricacies, volume variability and complex tax liabilities to traction across dispersed suppliers and facilities. Identify an automation platform able to:
- Extract and integrate complex multi-line invoices quickly
- Scale up instantaneously during peak seasons like machinery maintenance or inventory buildups
- Handle tax nuances across international jurisdictions
- Provide real-time visibility into AP health across the manufacturing group
While many software options exist, seek industry-specific AP automation experience.
The strategic benefits of AP automation for manufacturing companies
AP automation revolutionizes back-office processes into an agile competitive advantage for manufacturers seeking cost reductions and efficiency gains in growing disruption. Transitioning away from manual AP processes earlier in the digital transformation curve allows manufacturing companies to better optimize working capital, profitability and productivity with contemporary digital platforms.
Emphasizing the importance of digital transformation in the manufacturing industry
Modern manufacturers cannot afford to underinvest in intelligent automation and data integration. Early AP automation adoption equips firms both operationally and culturally to keep embracing emerging technologies - from cloud analytics to sensor-based maintenance.
By transforming key financial functions like procure-to-pay first, manufacturing companies lay the digital foundations and internal talent to get far ahead of the competition technologically for years to come. The time for AP automation is now.
As a manufacturer, disjointed accounts payable processes can strain working capital and hide excessive expenditures across facilities. But with Medius AP automation, you can optimize invoice processing, compliance, and cost controls to drive margins. Their solutions seamlessly integrate with major ERPs and supplier networks to transform AP efficiency. Contact Medius today to learn how automating accounts payable can help your manufacturing business capture discounts, improve cash flow, and enable growth.
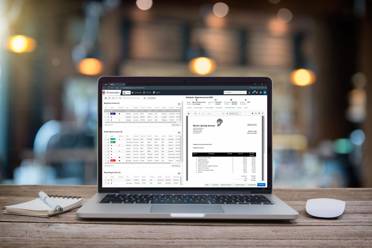